The construction of a bulkhead safeguards waterfront property from erosion by water. In addition, it can mark the boundary line between two property owners and prevent erosion from carrying onto other properties.
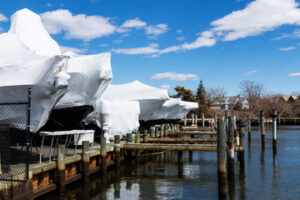
Bulkheads and seawalls may need to be repaired or replaced over time due to damage or deterioration. Signs of deterioration include visible twisting and rotation of a bulkhead’s concrete cap or gaps appearing between its berm and the rest of the structure. Kee reading the article below to learn more about Boat Dock Bulkheads.
A well-built bulkhead or seawall is highly effective in stopping coastal flooding and shoreline erosion. It also protects natural habitats behind the structure. In order to install a quality bulkhead, a homeowner should hire a professional marine contractor with experience in this type of work. During the installation process, an experienced contractor will take the necessary safety precautions to protect both workers and property. This will include using the proper equipment to excavate, assessing soil conditions and conducting an underwater inspection of the existing bulkhead.
There are a variety of materials available for bulkhead construction. These include stone, concrete, wood and metal. The best option is a vinyl seawall, which is made from long lasting, heavy duty, exterior grade vinyl that won’t corrode or rust. It is also easier to install than other materials. In addition, a vinyl seawall is more attractive than other types of seawalls.
Once the new bulkhead has been installed, it will be backfilled with materials that will provide additional support and create a level surface. Drainage systems can be installed to prevent water buildup behind the bulkhead. The area surrounding the bulkhead should be graded and landscaped to complete the project.
It is important to have a clear understanding of the cost breakdown before beginning a bulkhead construction or repair project. This includes the costs of materials, labor, permits and miscellaneous expenses. Homeowners should get estimates from multiple contractors before selecting a company to perform the work. They should be sure to choose a licensed and insured marine contractor with at least 2 to 5 years of marine building experience.
An experienced contractor will be able to design a bulkhead or seawall to suit the specific needs of each waterfront property. This will take into consideration factors such as wind and wave action, soil characteristics, property lines and drainage requirements. In addition, the contractor will consider the location of docks and other marine structures that may be adjacent to or in close proximity to the bulkhead. This will affect the type and size of foundation required to support the docks.
Maintenance
Depending on the material and construction of your seawall or bulkhead, the structure’s original specifications, strengths and installation quality will have an impact on how well it performs in the long run. As such, marine construction contractors that construct docks and piers can provide a cost-effective service for the inspection and maintenance of these structures as well.
As is the case with most waterfront property structures, a bulkhead or seawall needs regular maintenance. This is important to prevent problems that can exacerbate the need for expensive repairs or replacements down the road.
It is important to have your bulkhead and/or seawall inspected and maintained regularly by a marine construction contractor that is experienced in these types of structures. This will help to ensure that your bulkhead and/or seawall is in good condition and can withstand future weather events as well as anticipated vessel traffic.
A good inspection should include an evaluation of the structure below and above water. Ideally, a marine structural engineer will be involved with the inspection to identify potential deterioration and the associated risks of rehabilitation or replacement of the bulkhead or seawall. The American Society of Civil Engineers recommends routine above and below water inspections every five years for concrete, vinyl or composite pilings and every four years for unprotected timber or steel.
BERM & TOE FAILURE
Over time the stress of speeding boats and excessive wave action can cause the supporting berm on the water side of a bulkhead to erode or give way. This can create a gap between the toe of the bulkhead and the adjacent dock. This is usually a sign of excessive pressure in that area and can be corrected by rebuilding the berm with riprap or bagged concrete mixes if the issue is minor.
SLAB JOINT (SEAM) SEPARATION
This occurs when the joints between slabs of the bulkhead deteriorate and separate. This can result from uneven hydrostatic pressure on different sections of the bulkhead and is a common problem caused by inadequate drainage systems. There are new technologies that can repair these kinds of issues effectively.
Repairs
Over time, the cumulative stress of speeding boats and excessive wave action can cause the berm on the water side of a bulkhead’s toe to deteriorate, allowing it to slip outward. Signs that this has happened include visible twisting or rotation of the bulkhead’s concrete cap, cracks in the berm or gaps that open between the toe and rest of the bulkhead. If the toe movement is minor, a marine construction contractor can usually correct it by building up the berm and possibly supplementing it with riprap. For more serious toe movement, a marine construction contractor can typically install supplemental helical tie backs to keep the entire bulkhead in alignment and prevent premature deterioration and failure of this key structure on your waterfront property.
Another common problem that can occur is “joint separation.” This results from uneven hydrostatic pressure differentials between the panel joints, especially during low tides or heavy storm activity. Signs that this has happened include visible gaps between the panels and sometimes even the underlying soil. To prevent this from occurring, it is important to regularly divert storm water away from panel joints and to keep weep holes on the bulkhead’s water-side clean of sand and other soil that could restrict flow and contribute to hydrostatic pressure buildup.
In addition to these structural problems, a bulkhead’s upland piers can also experience premature deterioration and/or failure due to prolonged exposure. These problems are often the result of improper grading or stormwater runoff. To avoid this, a competent marine construction contractor should always check the underlying grade before beginning any work on the waterfront.
Keeping your bulkhead in good repair is an ongoing task that requires careful planning, monitoring and scheduling. A professional marine construction contractor can assist with a complete inspection, recommend the best repair/replacement strategy and provide an accurate cost estimate for any needed work.
When selecting a marine contractor, it is critical to make sure that they have the proper licenses and insurance coverage. Additionally, a good marine contractor will also have a track record of completing successful marine projects and will be happy to provide references and examples of previous jobs.
Replacement
A bulkhead is a major improvement that will protect your property and dock for decades. Make sure you get it done right.
Bulkheads are designed to decelerate erosion, water flow and facilitate construction of docks, piers or houses. They also deter boat damage, flooding and provide security and safety.
The design of a bulkhead is based on the soil conditions on the land side and the water depths to be maintained by the wall. A bulkhead is typically made up of a berm on the water side and a concrete wall on the land side. The berm and the concrete bulkhead walls are reinforced with rip-rap, which adds stability and strength to the structure.
When a bulkhead is installed it is constructed to withstand the maximum loads it will experience over its expected service life. If the conditions on or behind a bulkhead change such that it no longer meets the intended load capacity, then the existing bulkhead must be rehabilitated or replaced.
Over time the cumulative stress from speeding boats and waves can cause a bulkhead’s berm on the water side to deteriorate and give way, which can allow the toe of the bulkhead to slip outward. A slipped toe can be corrected by building up the berm and/or adding riprap, or it may be possible to place bags of dry concrete mix to stabilize the toe and restore the integrity of the bulkhead.
In some cases the existing seawall may be in good shape but the soil on the land side has eroded away and needs to be filled back in and re-compacted. This can be achieved using environmentally safe, high density polyurethane closed cell foam. These products are injected directly into areas of the bulkhead that need to be repaired and will seal, fill, stop further erosion and strengthen the existing panels of the bulkhead.
Another common problem seen in older seawalls and bulkheads is horizontal cracking of the panels caused by long term exposure to the elements at the water line. These cracks are normally caused by “hydrostatic pressure” that builds up in the panel material over a period of years. These cracks can often be corrected with modern crack repair techniques and proper drainage to relieve the hydrostatic pressure.